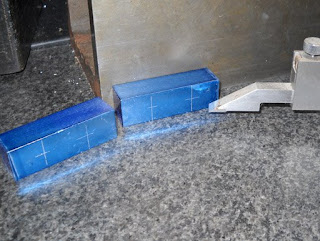
Marking the parts.
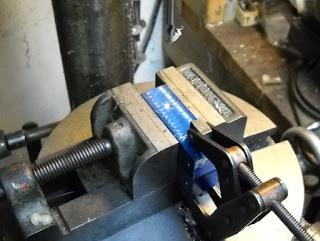
Spot drilling.
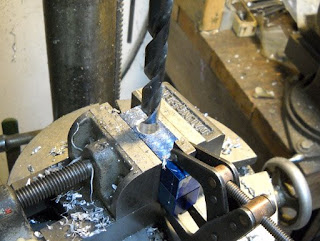
Drilling under 1/2"
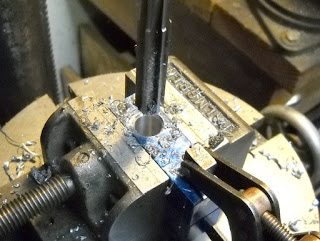
Reaming 1/2"+
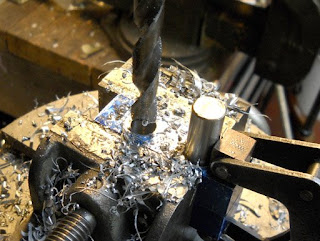
Flip the parts and use a dowel pin to align the previously drilled holes.
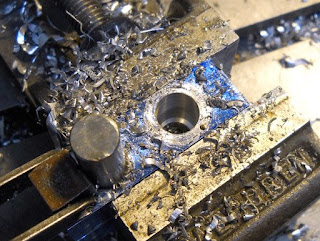
Reamed halfway through, the other part is just drilled to 1/2"-13 tap drill.
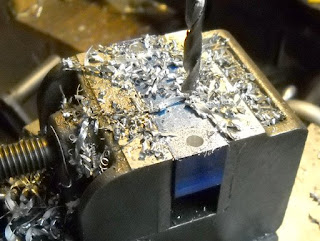
Some other holes..
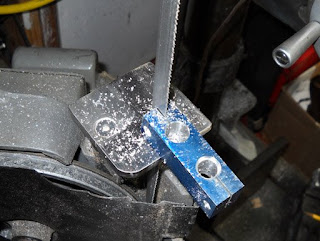
Slotting the parts.
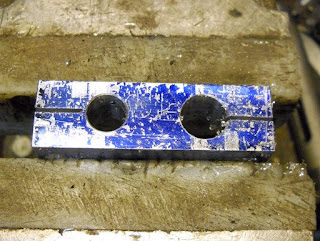
I almost slotted into the one hole that doesn't need slotting...
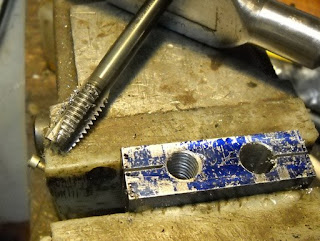
But instead needs tapping.
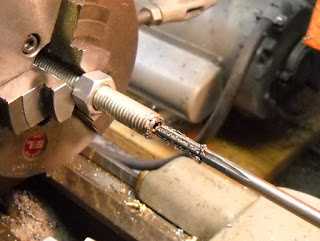
Drilled and reamed 1/4" the end of some 1/2" all thread.
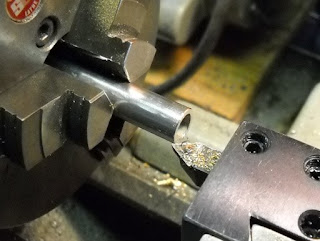
Facing some 1/2" diameter tubing.
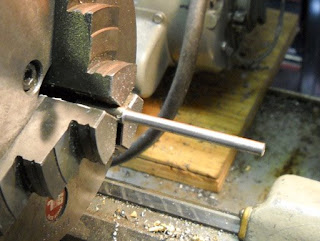
Making a 1/4" shank, roll pin punch.
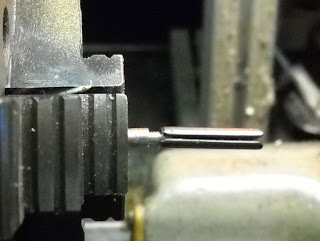
Small pilot on the end slips inside the roll pin.
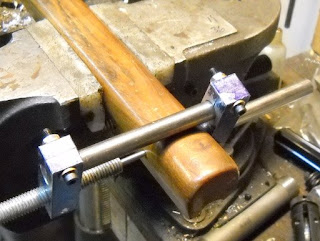
In use pushing out a roll pin from a Sheridan forearm.
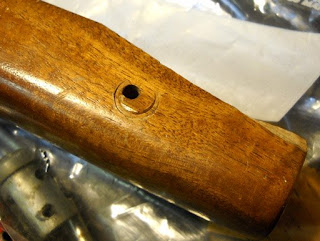
Hmmm. I suspected the end of the tube would do that. I'm not upset as you'll notice that the forearm already has a huge chunk out of it. I bought the Sheridan for $35.00 at a gun show. My plan is to make or replace the forearm.
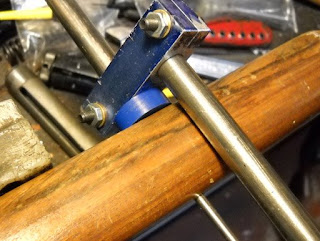
I made a slip fit delrin pad for the end.
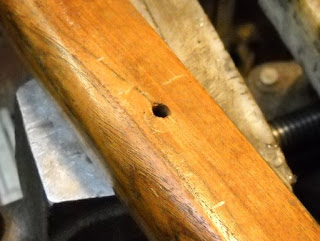
Just a slight pressure mark, I think I'll make a new pad from UHMW or other softer plastic.
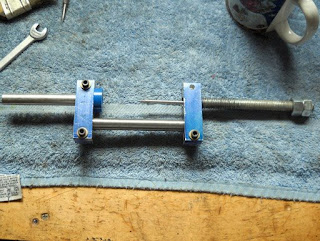
The screw needs a handle but two nuts with a wrench work fine for now.
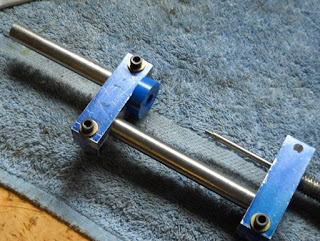
Adjustable...versatile...not a bad father's day project.
0 comments:
Post a Comment