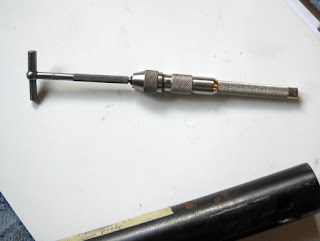
I needed a longer gage for measuring the bore of the tube. I hit on the idea of attaching a pin vise to the telescoping gage as an extension. I should invest in a bore gage at some point.
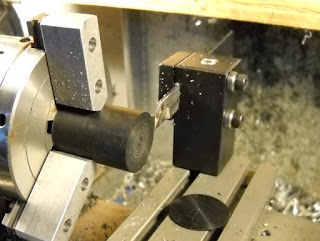
Cutting the face of some 75D urethane flat.
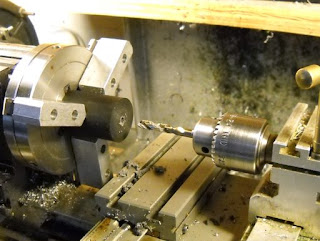
Drilling.
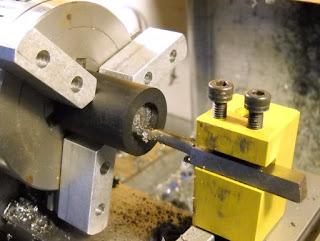
Boring the recess.
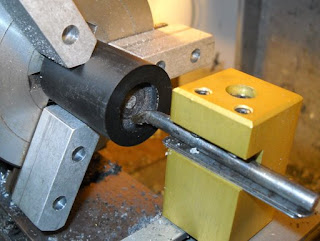
Grooving.
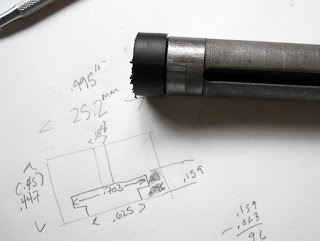
Snaps right on! Notice my precision drawing.
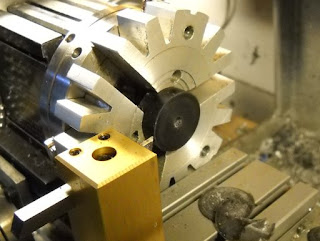
Facing to length.
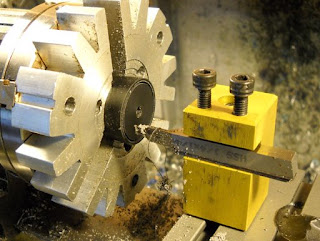
Grooving.
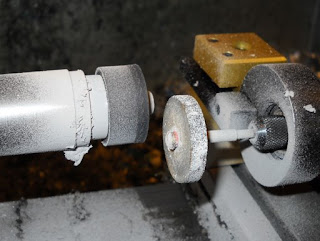
I decided to size the seal with a grinding stone in the dremel. Because I had cut the groove it generated a lip that tapered back to the body under the cutting force, which was ideal.
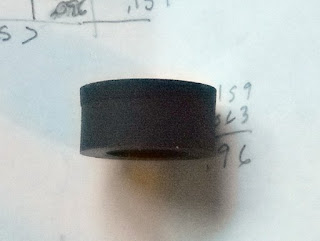
You can see the tapered front.
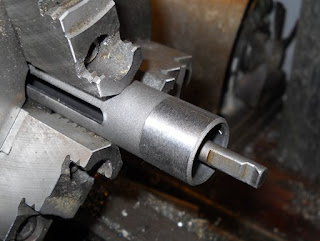
The piston was a bit rough at the front and back.
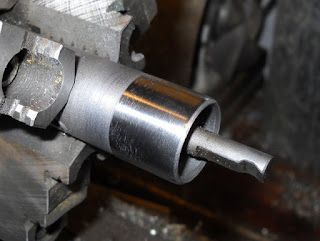
So I polished it up.
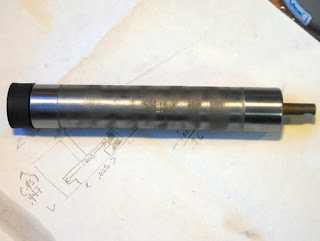
The machining on the piston is rough. The middle part doesn't matter as it doesn't contact the tube at all.
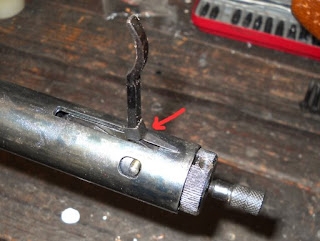
I only noticed that odd trigger spring contructed from flat spring steel when it fell out of the stock an onto the floor. This is where it goes. The rest of the rifle goes back together in reverse of disassembly.
The rifle was smooth but only about 320fps, which isn't good. So I tore it apart again and took another few thou off of the piston diameter. Put it back together and I'm getting about 520 fps with CPL's which is close enough to the 170 m/s (557 fps) of the factory spec.
Now to figure out a replacement front sight and rebuild the rear sight.
0 comments:
Post a Comment